Overhead allocation is an important aspect of the construction industry to manage their work better and make money. A business’s standard operational expenses appear throughout all tasks as indirect costs but remain necessary for everyday functioning. Proper cost distribution reveals the real expenses of every project to support pricing fairness, competitive tender selection, and wise company decisions.
This guide explains construction overheads and examines how to distribute them using square-foot data while presenting effective strategies for their use. When construction professionals learn these principles, they can estimate costs better and run their businesses effectively.
What are Overhead Costs in Construction?
A construction company needs indirect running expenses to maintain its business operations. Construction overhead expenses are not tied to individual projects because they benefit from all company operations, including administration costs.
Types of Construction Overheads
Fixed Overheads
These expenses stay unchanged even with changes in project size and work level. Such expenses stay consistent and follow simple planning procedures.
Example include:
- Office rent and Utilities
- Staff Member Fixed Salaries
- Insurance Premiums
Variable Overheads
The amount of variable overheads depends directly on changes in both project tasks and work volume changes.
These costs are more dynamic and include:
- Fuel and Transportation
- Cleaning Materials and Supplies
- Utility Expenses
Semi-Variable Overheads
A portion of these expenses remain stable as normal costs, and their usage levels increase expenses further.
For Instance:
- The leasing program includes fixed costs and utilization fees.
- Regular maintenance costs go up when repairs happen during that period.
Importance of Proper Allocation
Accurate overhead distribution helps companies track project costs correctly to increase profitability and win more contracts.
It is important because:
- Improved Profitability: When expenses are handled correctly, project bids account for all related costs, keeping profits steady and protecting money from disappearing.
- Enhanced Competitive Bidding: Accurate budget tracking allows businesses to set project costs that match market demands, increasing their chances of winning new contracts.
- Financial Transparency: Transparent cost breakdowns benefit all project stakeholders, who trust the allocation systems when making financial decisions.
- Resource Optimization: Businesses can save money by finding what expenses cause the most costs and then make better use of their resources and funds.
When overhead costs are listed correctly, projects succeed better for businesses and make more money.
Standard Overhead Allocation Methods for Contractors
Overhead Allocation helps projects show their real cost structure and protects profit margins. Project Managers choose overhead cost allocation methods based on th multiple project characteristics, including size, employee requirements, and equipment utilization.
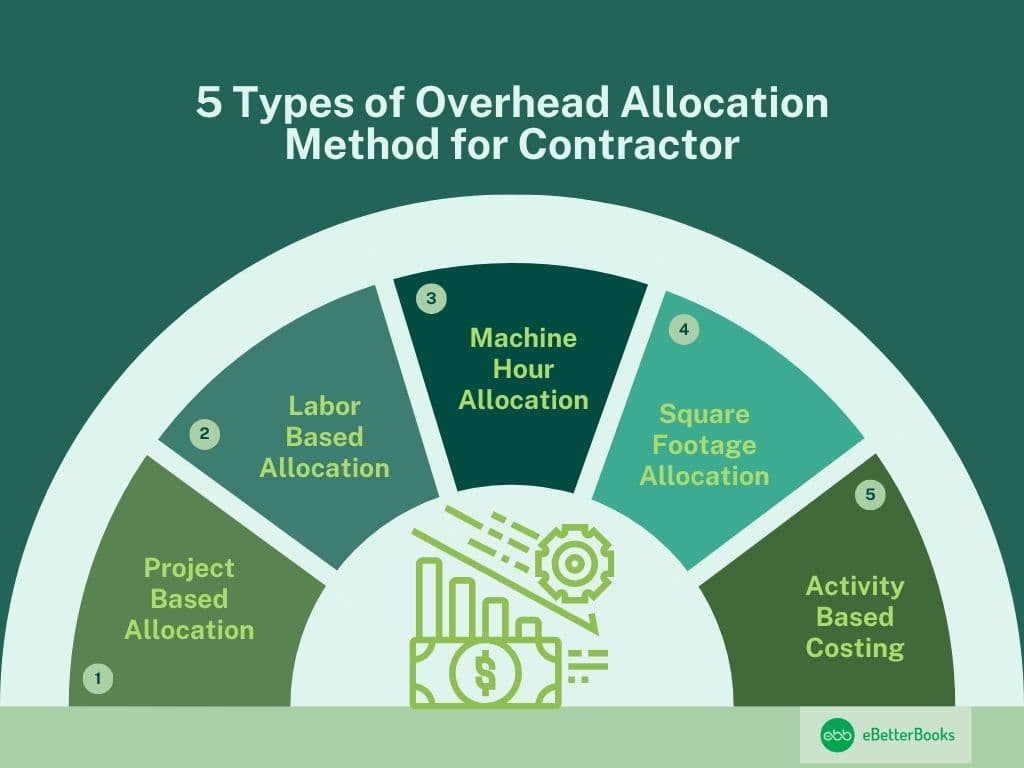
Project-Based Allocation
The project-based system divides overhead expenses according to project scale and value. Overhead spending is distributed based on how expensive or large each project is.
Example: Unlike small renovation projects, which need limited planning and coordination, a large high-rise construction project demands more overhead resources.
Labor-Based Allocation
When a project involves many workers, overhead expenses are divided proportionally between projects according to the number of hours they worked or earned.
Example: For setting overhead costs, the size of labor hours directly affects how much a project receives.
Machine-Hour Allocation
Overhead costs are distributed according to how much a project uses equipment.
Example: A project using cranes and excavators for 100 hours pays more in overhead expenses than a project using the same equipment for 50 hours.
Square Footage Allocation
The overhead allocation method uses project floor space as a measurement tool. This system works best for large-scale operations that consume space because their site usage affects their indirect costs.
Example: The overhead cost distribution will be larger for a project spanning 10,000 square feet than one occupying 5,000 square feet.
Activity-Based Costing (ABC)
ABC divides overhead costs according to project activities that trigger costs, including project planning, materials handling, and safety checkups.
Example: Complex projects that need extensive organizing need extra overhead expenses than straightforward projects require.
Through proper selection of cost allocation methods, businesses can distribute expenses fairly between their projects.
Pros and Cons
Every allocation system brings specific advantages and specific problems to construction projects.
Here’s a closer look at their suitability for construction projects:
Method | Pros | Cons |
Project-Based Allocation | Resource costs are distributed evenly based on project dimensions and expenses. | The cost distribution system allocates uneven amounts to expensive projects. |
Labor-Based Allocation | This method gives reliable cost results for builders who depend heavily on worker hours. | This approach gives poor results when projects use few workers and plenty of equipment. |
Machine-Hour Allocation | Large projects with equipment need to pay their expected share of operational expenses. | Projects share the same machinery, making tracking overhead costs more difficult. |
Square Footage Allocation | The basic format works best to spread overhead costs related to utility usage when space runs short. | The method depends on cost relationships between space usage, which could yield incorrect results. |
Activity-Based Costing | Companies can identify and cut unnecessary expenses by matching costs precisely to activity types. | Tracking needs precise details, which consumes many resources. |
Step-by-Step Allocation Guide of Overhead Costs
Producing correct cost distributions across all projects requires a complete plan to track overheads correctly.
Follow these steps for precise overhead allocation:
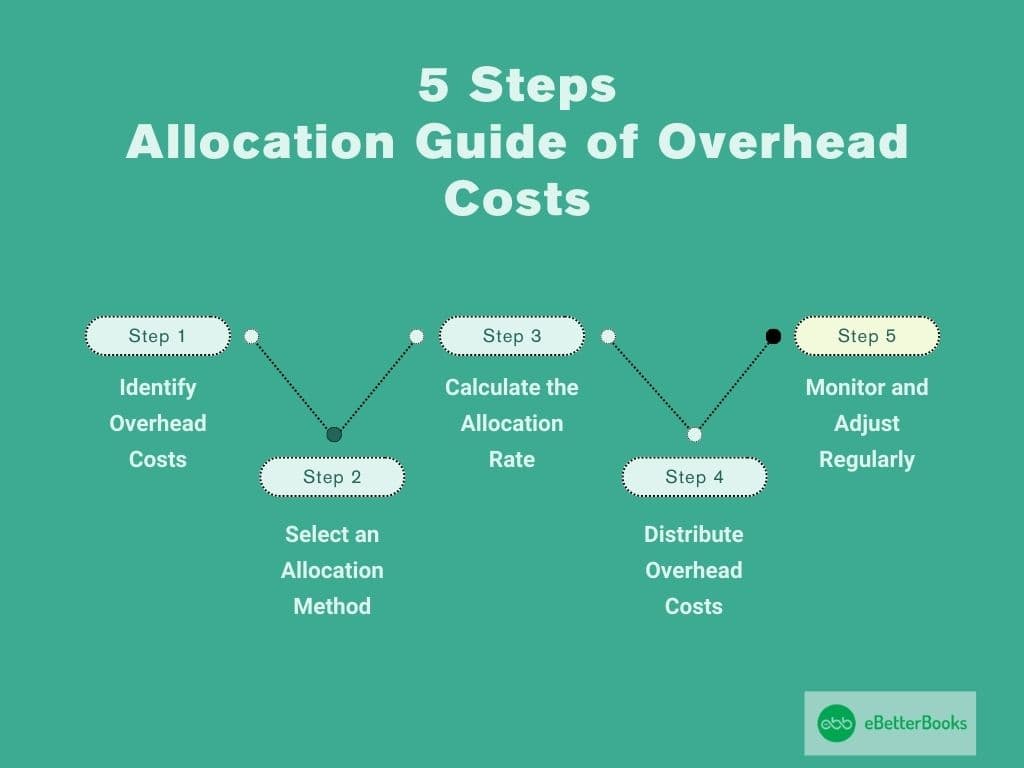
Step 1: Identify Overhead Costs
Organize and categorize overhead costs between fixed, variable, and partial variable components.
Example: The breakdown includes rent as fixed costs, fuel expenses as variable items, and equipment maintenance expenses between fixed and variable.
Step 2: Select an Allocation Method
Pick the allocation approach that matches your project needs and cost drivers.
- For labor-intensive projects: Use labor-based allocation.
- For space-driven projects: Based on space use, establish a square footage basis for allocation.
Step 3: Calculate the Allocation Rate
Decide your allocation rate according to your preferred technique.
Example for square footage:
Allocation Rate = Total Overheads / Total Square Footage
Step 4: Distribute Overhead Costs
Apply the rate to each project:
Overhead Allocation = Allocation Rate x Project Size
Step 5: Monitor and Adjust Regularly
Regularly examine how projects use overhead costs when drivers or needs change.
Revise your rate when changes happen to big cost drivers.
When a construction company uses this defined system, it distributes overhead costs fairly between projects.
Useful Tips for Better Overhead Allocation
Business decisions that focus on costs plus practical methods make accurate overhead allocation.
Here are some tips to streamline the process:
- Invest in Technology: There is construction management software that automatically tracks overhead costs and distributes them correctly. These construction software tools make difficult financial computations easier.
- Understand the Project: Study how each project uses resources differently, including its personnel demands, equipment use, and physical needs.
- Regularly Audit Costs: Regularly check overhead expenses to guarantee proper and correct allocation tracking.
- Craft a Special Method: Instead of using a typical method for all projects, customize your process and pick a cost allocation process that matches the project requirements.
- Collaborate with Teams: Meet with your project team members, including professional financial experts, to obtain the correct cost distribution data.
- Plan for Contingencies: Add a special fund to cover unplanned costs so projects don’t fall below budget.
These practices boost overhead accuracy and speed while showing project financial performance accurately.
Conclusion
Using overhead expenses to cost projects properly is a basic part of running construction operations effectively. Every business benefits from maximizing efficiency by choosing effective overhead allocation methods and following consistent steps to track construction costs accurately. Various project cost methods, including project-based and square footage models, allow different construction projects to get the right amount of overhead support.
Financial control systems and audit procedures, combined with technology adoption, clearly show project costs and help businesses use resources more effectively to make money. To thrive in a tough construction market, businesses need good financial strategies and effective project management.