The manufacturing industry relies on cost accounting through overhead allocation as its fundamental principle. This approach allocates expenses that are not directly used in production, such as utilities and depreciation, including supervisory salaries, to the products under manufacturing.
Coststhath supports manufacturing operations that exist independently from individual units yet remain indispensable to keeping production running smoothly. Businesses experience financial losses when they improperly allocate their production costs because they underestimate actual operational expenses. Efficient overhead allocation helps manufacturers achieve accurate costing, profitability analysis, and resource optimization.
What are Manufacturing Overheads?
Running a business under manufacturing incurs expenses for indirect production-related costs, which cannot be traced directly to individual production units. These costs diverge from direct costs because they get utilized throughout every production operation.
Common categories include:
- Factory Utilities: The factory uses electricity to power machinery, and heating requires gas, while the production process needs water for cleaning applications. Production volume dictates the level of these expenses.
- Equipment Depreciation: All machinery and tools experience value depreciation throughout their service life. Equipment depreciation allocates an equal proportion of cost between all manufactured products reliant on that equipment.
- Maintenance Costs: Equipment must be maintained and repaired regularly to preserve optimal operating conditions. Broken maintenance routines reduce production efficiency.
- Indirect Labor: Employees who serve the factory by functioning as factory supervisors and security personnel, including cleaning staff, receive wages as part of this category.
- Miscellaneous Overheads: Machinery depreciation forms part of factory costs alongside insurance expenses, property taxes, and manufacturer-supplied lubricants and learning materials.
Costs from these various sources are merged before being distributed among products through suitable allocation approaches, which prevent any product from being overpriced or undervalued.
The Concept of Allocating Manufacturing Overheads
A chosen allocation base defines how companies distribute indirect costs pooled from manufacturing operations to individual products or production jobs. The total accuracy of overhead allocation requires correct estimation between the initial application of incurred overhead and the final reconciliation steps.
- Estimated Overhead: Businesses use estimates derived from historical tracking data and projected business activities to predict their complete overhead costs for a certain period in advance. The predicted overall budget of $30,000 emerges when a company forecasts its $10,000 factory maintenance bills alongside its $20,000 predicted utility payments.
- Applied Overhead: Manufacturing facilities allocate their overhead expenses between products through predetermined cost rates during production operations. Applied overhead allocation allows businesses to maintain real-time cost tracking, which prevents significant delays when making operational decisions.
- Actual Overhead: A comparison is made between actual overhead expenses and previous allocations at the end of the accounting period.
Variances are then reconciled:
- Under-Applied Overhead: It occurs when the costs calculated using application methods are lower than those recorded in actual reporting. Flawed allocation approaches result in untracked expenses that require cost adjustments to achieve accuracy.
- Overapplied Overhead: It occurs when the costs applied exceed the actual costs, resulting in higher-than-accurate product costs.
Reconciling these differences between actual costs and applied amounts leads to correct financial statement reporting and provides precise profit visibility.
Allocation Rate for Manufacturing Overheads
Overhead allocation establishes the distribution method used for cost transfer from production to units of finished goods through cost drivers like machine hours or labor hours.
The formula is:
Overhead Allocation Rate = Total Estimated Overhead Cost / Total Allocation Base
Example:
Estimated Overhead: $100,000
Allocation Base: 5,000 machine hours
Allocation Rate: $100,000 / 5,000 = $20 per machine hour
To allocate overhead:
Multiply the allocation rate with the actual base usage.
Final adjustments regarding variances must occur at a periodic conclusion.
Application: Using 1,000 machine hours results in an allocated overhead cost of $20,000. Break-even analysis uses this method to distribute overhead costs according to actual resource utilization during the production run.
Methods of Overhead Allocation for the Manufacturing Industry
Multiple allocation methods exist because each aligns with different production requirements in modern manufacturing operations.
Each method ensures overhead costs are assigned fairly and accurately:
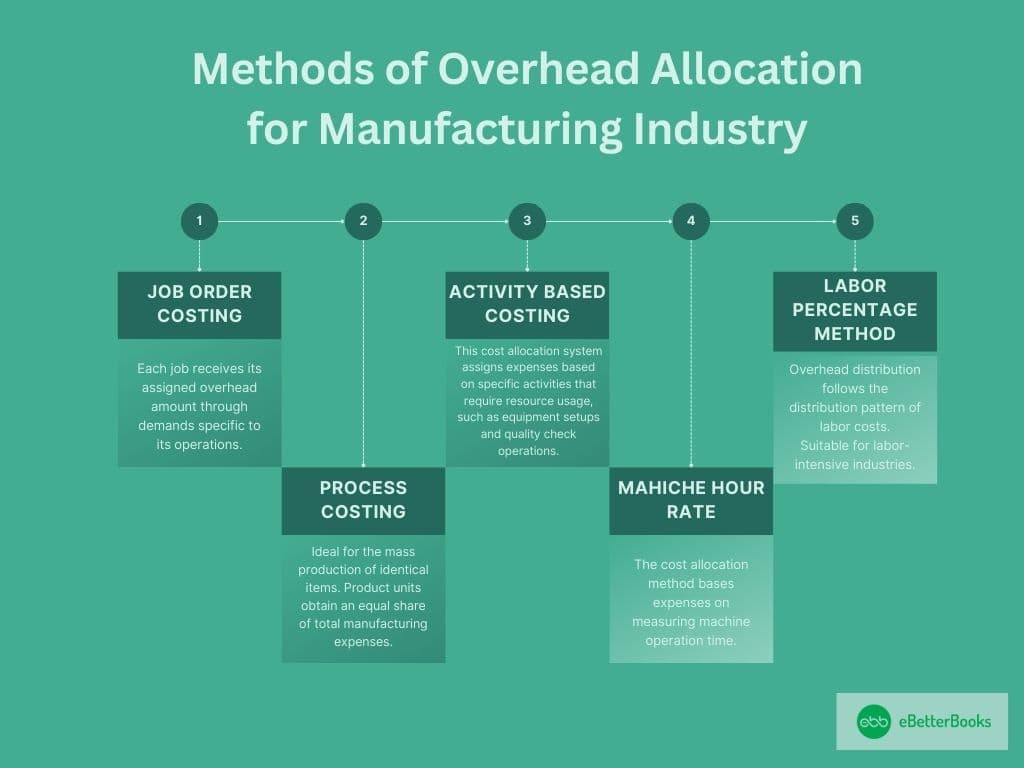
Job Order Costing
- Suitable for custom or small-batch production.
- Each job receives its assigned overhead amount through demands specific to its operations.
Example: The custom chair production process at the furniture manufacturer bases its assignment of overhead costs on the duration of work and utilized resources for each order.
Process Costing
- Ideal for the mass production of identical items.
- Product units obtain an equal share of total manufacturing expenses.
Example: During a production period, each bottle produced by a beverage factory receives an equal share of the total overhead expenses.
Activity-Based Costing (ABC)
- This cost allocation system assigns expenses based on specific activities that require resource usage, such as equipment setups and quality check operations.
- Better accuracy results from clearly understanding which factors cause expenses to rise in a system.
Example: A car manufacturer uses the number of vehicles passing through paint shops to distribute their associated overhead expenses.
Machine Hour Rate
- The cost allocation method bases expenses on measuring machine operation time.
- Useful for industries reliant on automation.
Example: A factory streaming metal parts allocates overhead costs to the total CNC machine processing time for individual products.
Labor Percentage Method
- Overhead distribution follows the distribution pattern of labor costs.
- Suitable for labor-intensive industries.
Example: A textile factory distributes its overhead costs using total wages paid to all workers who participate in manufacturing operations.
Manufacturers who select proper cost allocation methods achieve fair and efficient distribution patterns, which inform business decisions.
Step-by-Step Guide to Allocate Overhead Costs
Various coordinated methods guide the proper distribution of overhead expenses to products.
Follow these steps to allocate overhead in a manufacturing environment:
Step 1: Identify Total Overhead Costs
- Identify every indirect expense incurred during product manufacturing. Total overhead costs include factory utilities and equipment depreciation, as well as maintenance and indirect labor expenses. During month-long operations, when indirect costs amount to $50,000, these funds constitute the entire overhead pool.
Step 2: Select an Allocation Base
- A cost driver that accurately tracks the connection between overhead expenses and manufacturing actions should be selected for allocation usage.
Common bases include:
- Machine hours for automated processes.
- Direct labor hours for labor-intensive production.
- A product volume serves as the basis for allocating costs in mass production scenarios.
Step 3: Calculate the Overhead Allocation Rate
Use the formula:
Overhead Allocation Rate = Total Estimated Overhead Cost / Total Allocation Base
When analyzing $50,000 total overhead through 10,000 total machine hours, the overhead allocation rate becomes $5 per machine hour.
Step 4: Allocate Overhead to Products
- When determining costs for each product, multiply the actual allocation base usage by the overhead rate. For example, a product with 500 machine hours will receive $2,500 in allocated overhead costs by multiplying machine hours (500) by the overhead rate ($5).
Step 5: Adjust for Variances
- The company must evaluate applied overhead expenses versus actual overhead costs during the period’s end. The financial records need accurate reporting, so any under-applied or over-applied overhead needs to be properly reconciled.
This structured method leads to fair cost dispersion together with improved decision-making outcomes.
Practical Example of Overhead Allocation
For the illustration, we will examine a furniture company that produces chairs and tables.
Step 1: Total Overhead Costs
Total overhead costs for the month include:
- Factory utilities: $10,000
- Maintenance: $5,000
- Indirect Labor: $15,000
- Total Overhead: $30,000
Step 2: Allocation Base
- The business allocates expenses based on machine operating time. During this month’s operations, the company used 1,000 machine hours.
Step 3: Overhead Allocation Rate
- For rate calculations, several essential steps are required: Overhead Total operates while Machine Hours Total divides.
The overhead cost rate amounts to $30 because $30,000 is divided by 1,000 machine hours.
Step 4: Allocate Overhead
- Chairs: 400 machine hours × $30 = $12,000
- Tables: 600 machine hours × $30 = $18,000
Step 5: Adjust for Variances
- Since the actual overhead cost was $29,000, the business incurred an overapplied overhead of $1,000 because the month-end overhead was initially calculated at $30,000. The financial statements incorporate this expense adjustment.
Technological Tools for Overhead Allocation
Modern technology achieves two benefits for overhead allocation – it increases process efficiency while maintaining precision.
Key tools include:
ERP Systems
- SAP and NetSuite: Real-time overhead cost tracking becomes possible through automated allocation that receives integrated department data.
- Oracle ERP Cloud: This system provides sophisticated analytics features that help detect underlying cost causes and reveal operational inefficiencies.
Cost Accounting Software
- QuickBooks: This system supports overhead cost tracking and allocation for business operations of various scales beyond large enterprises.
- FreshBooks: The system streamlines the management of indirect costs while providing users with a comprehensible presentation interface.
Activity-Based Costing (ABC) Tools
- Specialized software applications Prophix and CostPerform reveal activity-based cost drivers to achieve better overhead allocations.
Strategic decision-making benefits from improved resource utilization made possible by implementing technology systems.
Ways to Reduce Manufacturing Overhead Costs
Manufacturers can optimize operations and reduce overhead costs through the following strategies:
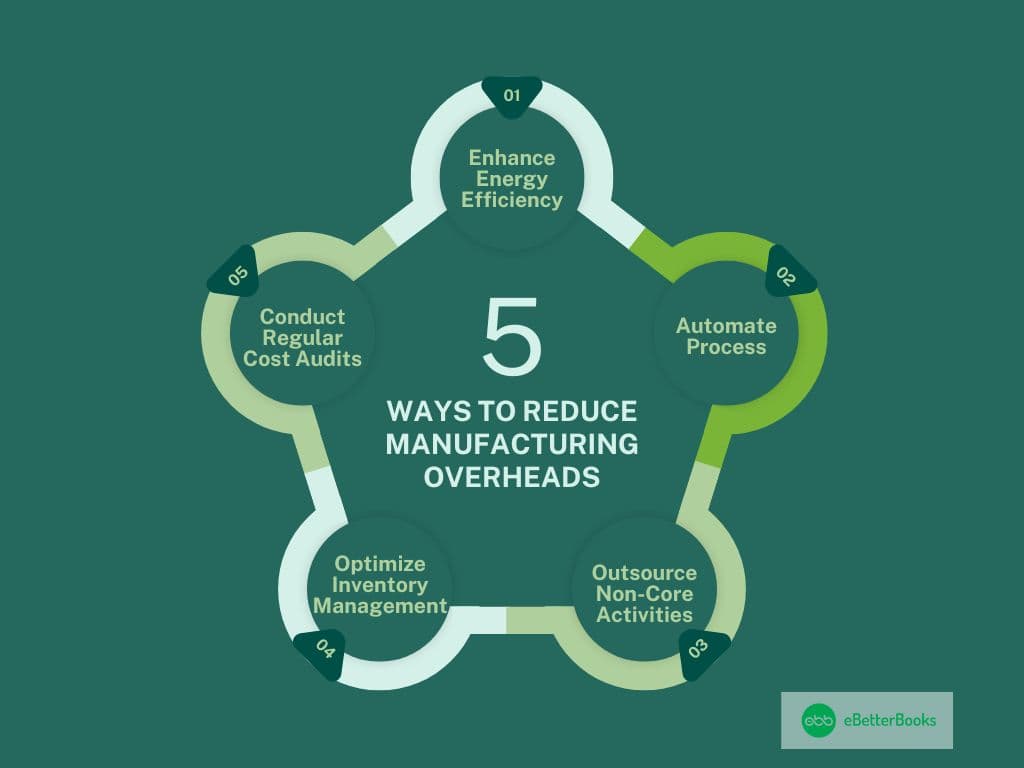
- Enhance Energy Efficiency: Using more efficient equipment will decrease utility charges. To manage the light utilization in the production area, a combination of motion sensors and timers should be used.
- Automate Processes: Automation using AI and robotics enables manufacturers to decrease labor-intensive workloads, reducing their short-term expenditures. Implementing IoT technology tools allows monitoring of machinery status to prevent operational interruptions.
- Outsource Non-Core Activities: Specialized vendors should take over maintenance and security operations within your company. The organization should dedicate its resources to its fundamental production processes.
- Optimize Inventory Management: A just-in-time inventory control method must be implemented to minimize storage expenses. The implementation of inventory management software creates protection against both overstocking and understocking situations.
- Conduct Regular Cost Audits: Regular analysis of overhead costs helps companies find specific areas where waste exists. Suppliers should be offered better conditions for utility services and maintenance contracts.
An optimized approach to overhead expenses results in higher profits while maintaining existing product standards.
Conclusion
Businesses need precise overhead allocation methods to uncover actual manufacturing costs. By implementing the proper tools, methods, and strategies, businesses can achieve fair cost distribution, improved pricing accuracy, and profit maximization. Through technology adoption combined with cost-reduction strategies, manufacturers can strengthen their financial health, thus achieving better success in market competition.